
Industry 4.0 entry barriers; helping you capture your future value
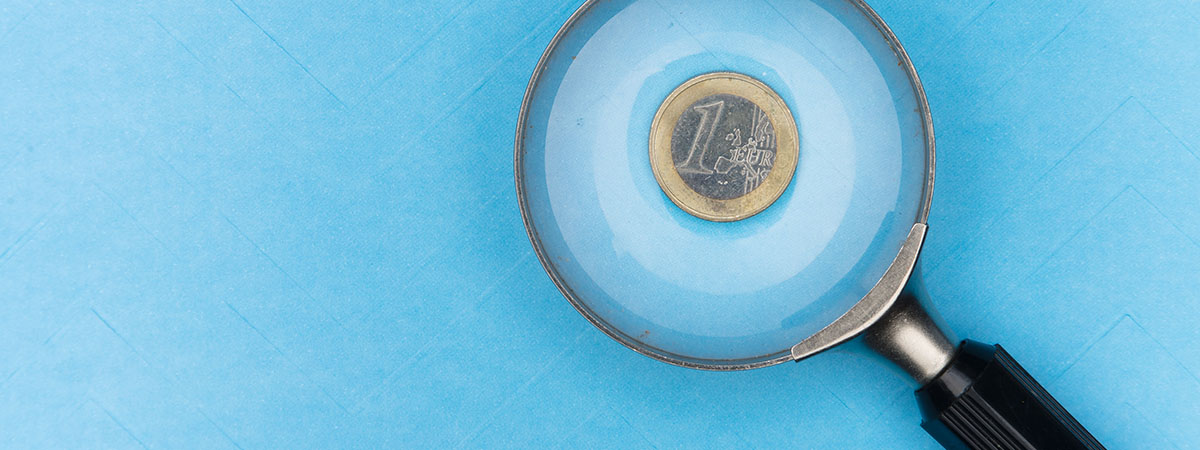
When searching the internet and other sources for practical information on applying Industry 4.0 principles and technologies, the overabundance of information and solutions can be overwhelming. White papers and academic publications can sometimes be overly theoretical or too academic to be of any use at a decision making, operational or factory floor level.
Likewise, browsing the ever-increasing options of complex automation software platforms and new ‘smart’ equipment available for purchase can often be intimidating and cost prohibitive to new players in the world of digitalisation looking to maintain a competitive edge in the future. The barriers to entry into digitization are not only due to the upfront costs involved, but also knowing how to adjust your workforce’s knowledge and skillsets as well as information flow between various entities (both human, computer and machines!). Compound this with differences in company process and the different levels of operations and one can begin to understand why a solution that looks to maximise and capture value through digitalization can’t be found until the complexities of the problem are well understood!
The main reason that searching for the next step of modern manufacturing can be daunting, can be put down to this fact that it is near impossible to find any ‘one size fits all’ product or solution that many hope to find. Unfortunately, it is far more complex than finding that magical “Industry 4.0 Software starter pack”. There is far too much variation and points of difference at various levels of today’s organizations to apply any single solution to manufacturing operations across different manufacturing environments. Variations in physical equipment and digital networks used, inter and intra organizational communication and interaction and difference in products and services are all factors that vary greatly between individual firms.
Fortunately, AM Center are here to help your company apply the latest Industry 4.0 research to your company. Capturing this available future value through digitalisation can occur at various level. Whether you are looking into reducing labor costs some entry level smart automated equipment that be built upon in the future or looking at a complete intelligent system overhaul or business proposition, a first step that should be considered is an Industry 4.0 Audit. AM Center I4.0 Audit is one of several Industry 4.0 based services developed and offered by the Fraunhofer Project Center.