
Exploiting the potential of industrial 5G
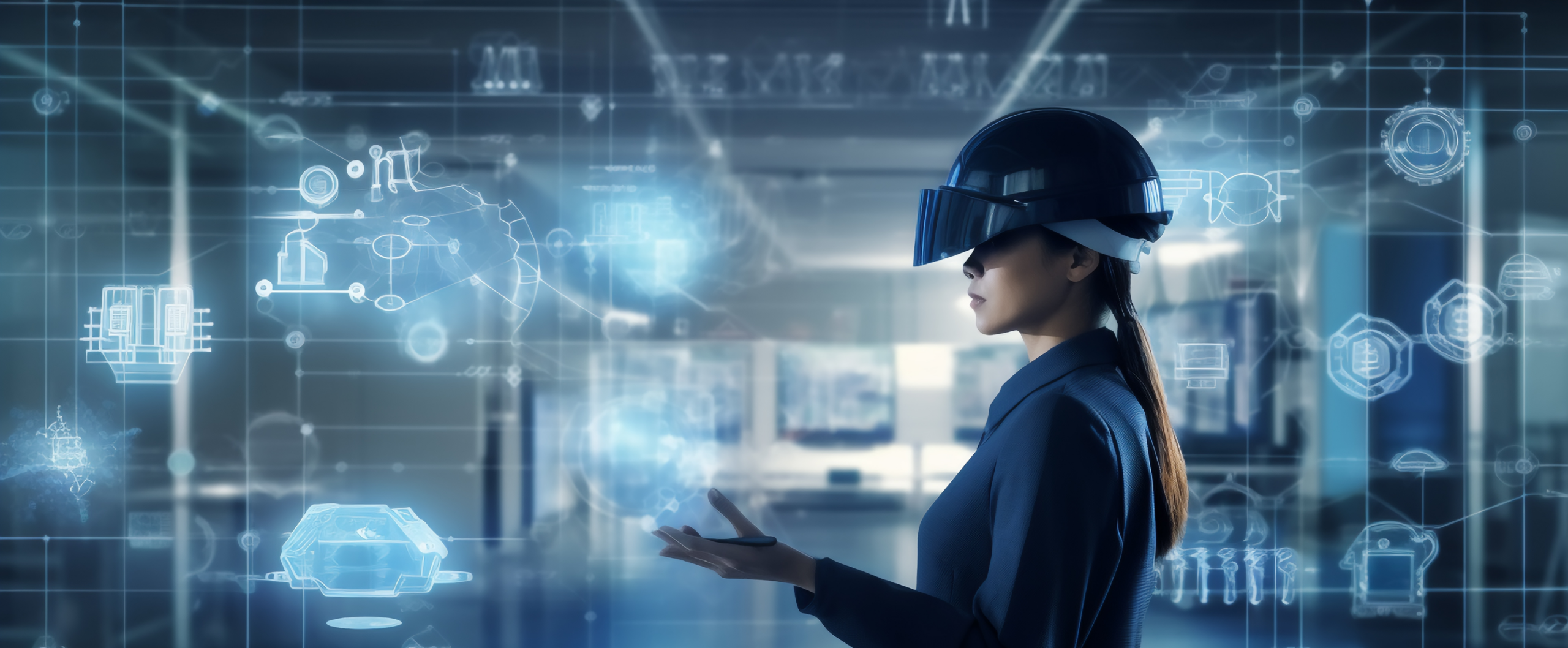
5G is a critical enabler of the fourth industrial revolution. In this article, we explore three ways it enables us to build the factories of the future.
Hyperconnectivity is a defining characteristic of the fourth industrial revolution. Connectivity is a critical enabler of many innovative technologies driving the factory of the future, such as IoT, augmented reality, and edge computing. After all, operations like predictive maintenance and digital twinning depend on the near real-time exchange of data. This in turn comes with much higher bandwidth, higher capacity, and lower latency requirements than what can be delivered by older communications systems and protocols.
The industrial 5G advantage
For local connectivity, copper wire or WiFi remains standard, but they suffer from similar problems, especially in very large factories. For example, even if you have fibre to the premises, you are not going to be able to realise all the benefits of fibre-optic connectivity if your internal network infrastructure spans thousands of square metres and uses copper wire or WiFi.
5G completely redefines mobile connectivity with greatly enhanced bandwidth, lower latency, and support for network segmentation. With peak download rates reaching 20 Gb/s and less than 1ms of latency, 5G can support real-time communications at massive scale. For example, a single 5G network can support hundreds of connected devices, making it possible to support data collection and predictive maintenance in even the largest factories. Another key benefit of 5G for manufacturing is the ability to create private network segments for securing data in transit and prioritising traffic on a per-use case basic.
Other potential use cases for 5G include automated guided vehicles used in drone inspection, wearable augmented reality technology, and logistics tracking. By deploying 5G technology across the entire manufacturing value chain, factory manages can maintain complete visibility in a way that would otherwise be impossible when relying solely on previous-generation mobile or fixed-line infrastructure.
Overcoming uncertainty
In spite of the clear advantages of 5G, 55%1 of manufacturing enterprises still have no plans to deploy it due to uncertainty. Chief among their reasons are lack of understanding of ROI, unpredictable costs, and a lack of technical knowledge. Furthermore, 67% of manufacturers believe that vendors themselves lack a coherent vision for deploying 5G. In other words, it’s proven difficult to set apart the help from the hype.
Most of these concerns are legitimate. After all, since 5G uses a different wavelength than 4G, it requires new hardware before widespread deployment can occur. More connectivity also means a larger cybersecurity attack surface, thus requiring a new level of protection. Almost a third of manufacturing decision makers claim security concerns are a primary reason of their hesitance towards adopting 5G.
Fortunately, none of these challenges are insurmountable. Moreover, the enormous financial incentives of 5G are simply too important to put on hold. That’s why it’s important to think of 5G not as a bolt-on technology, but a complex ecosystem comprising many moving parts. This in turn requires a strategic approach in which the concepts of resilience, employee experience, and sustainability are fundamental to the broader vision.
The Fraunhofer Innovation Platform brings together industry experts to offer powerful solutions across the entire manufacturing value chain. Assess your 5G opportunity with us today!
Source
1.E&Y: https://criticaleye.com/inspiring/insights-servfile.cfm?id=5459
Bitkom: https://www.bitkom.org/sites/default/files/2019-05/190515_bitkom_charts_pk_5g.pdf
With a strong background in electrical engineering and certified Software Architect, Barry te Dorsthorst has established himself in the field of 5G and industrial connectivity. As the FIP-AM@UT in-house lead for 5G initiatives within the Advanced Manufacturing Centre, his work revolves around pioneering solutions that drive operational efficiency and shape the future of manufacturing.