
The Challenges of Recycling 3D-printing Waste
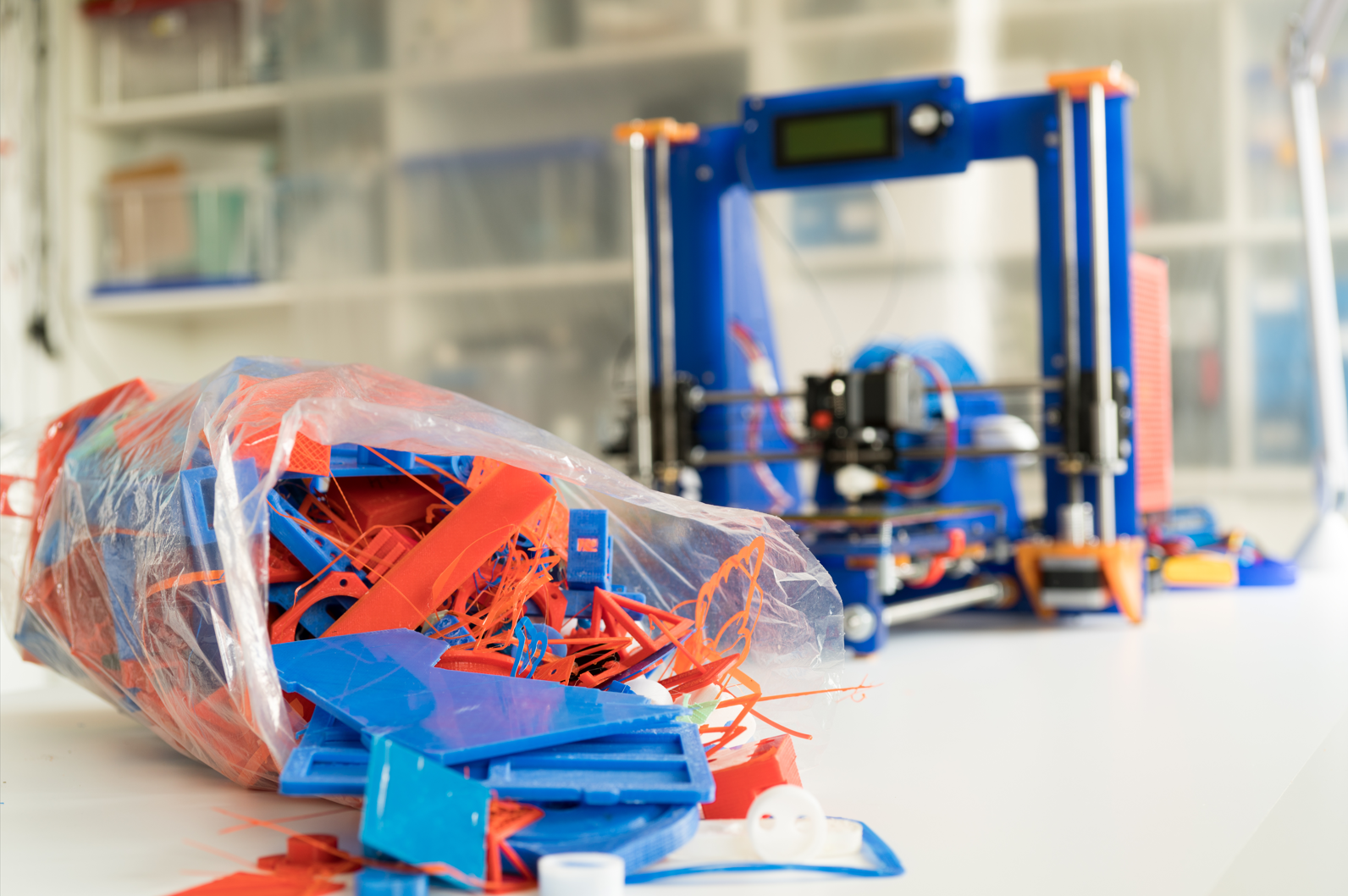
As wonderful as innovations can be, they also come with new challenges. While 3D-printing is known for its potential in material efficiency, there is still some waste generated. In a time of growing environmental focus, addressing the challenge of recycling 3D-printed waste is becoming increasingly more relevant.
So, what is 3D printing?
For those unfamiliar with Additive Manufacturing (AM), commonly known as 3D-printing, a brief introduction: unlike traditional manufacturing processes which remove material, AM machines add material on a layer-by-layer basis. There are many types and technologies within AM, which can utilize a broad range of materials like polymers, metals, composites and more. This time, we will focus on the FFF/FDM printing technique where a polymer wire (filament) is heated and extruded through a nozzle.
Figure 1, principle of FFF/FDM-printing.
Arguably, 3D printing has only taken off in the last decade, steadily gaining ground in the manufacturing industry and is expected to keep growing. Roughly 10 years ago, 3D-printing quality had much to be improved and could still be considered more suitable for hobbyists. A good example of this is filament, which used to be difficult to get in good quality. Back then, some people even used grass trimmer lines as 3D-Printing filament, and professional AM machines capable of producing higher quality products but were out of reach for the common consumer. Today, quality, accessibility, and ease of use of printers and filament have improved significantly. AM has now become an indispensable technology for diverse industries and educational institutions.
FDM printers can create products with intricate geometry, can use a variety of polymers and composite materials, while only needing a low initial investment. Though not always suitable for serial mass production, they excel at making prototypes rapidly and can even be used for producing functional parts in smaller volumes.
Even though FDM is a material efficient technique, waste is still produced in the form of failed parts and smaller debris, consisting of support and adhesion structures, flow calibration lines and purged material. While one print job may only generate a couple of grams of waste, it will accumulate quickly over time. To make 3D-printing more sustainable, certain challenges will have to be addressed to reduce the impact of an emerging technology.
Let us talk about filament waste and recycling it
One of the most popular filaments for FDM machines is Polylactic Acid (PLA), which is a biopolymer made from renewable biomass and a great alternative to some fossil-based plastics. Many other polymers can also be used, which for example may be fully renewable and compostable in nature (PHA), fossil-based (ASA, PETG), composites (Nylon + glass fiber, PC + carbon fiber) or special blends (glow in the dark). Finally, pigments may be added for color to any filament.
You can well imagine the challenge of recognizing one filament from another, let alone when it is in a general waste stream. For this reason, many polymer parts have recycling emblems and text on them, clarifying what they are made of. Sadly, most 3D-printed products and openly accessible 3D-models, do not have these emblems. Taking PLA as an example, which is recyclable and industrially compostable, will see its sustainability potential go up in flames (literally) because of this. While it is possible to add emblems to models in CAD/CAM software, it is still a manual and user-dependent process.
Adding on to this challenge, the earlier mentioned small debris and failed products will just not be recognizable in a general waste stream and will have to be sorted out by the user to give it a chance at recycling.
Figure 2, our own collected PLA waste at FIP to be recycled later.
The solutions?
There is no single approach that will solve the problem, but we have a few ideas. For instance, instead of filtering the waste out of a large stream, the user could return the waste to filament factories directly for recycling, repurposing, or disposing of it properly. Whether or not filament can be recycled depends on filament type, the composition of it, as well as the material quality after recycling. This approach not only will help return the product to a facility that has the expertise for (re)making filament, but also eliminates the need for waste separation measures in the waste stream. So why aren’t we already doing this?
Protected information about the composition of filament, cleanliness and contamination of the sorted waste and gathering enough volume to start a recycling process are examples of challenges the industry is facing. There are filament intake services available, but they’re scarce and difficult to find. To turn filament recycling into a common practice, the process must be smoothed out before it becomes common and viable for more filament producers. If it is inevitable to dispose of such filament, it is important to raise awareness around the implication of plastics and microplastics in waste streams. But how do we do that?
Fuelling education and improving legislation
Informing and educating users is essential to reduce the impact of polymers on our environment. Currently, some filament vendors use arguably vague terms like “bio-based” or “compostable”, which leave room for interpretation. Moreover, the term “compostable” refers to the product being either compostable at home or only in industrial settings. However, both processes are largely different and require very distinct conditions. Since 3D-printing is a growing market and beginner-friendly, (starting) users will be unaware of the material specifics. Clear information and proper legislation will therefore be required to avoid misleading consumers. The EU does have advice and some standards in place regarding when polymers may be named biopolymers or compostable polymers, but they are not all legally binding. (source: https://environment.ec.europa.eu/topics/plastics/biobased-biodegradable-and-compostable-plastics_en#law). This opens the opportunity for filament manufacturers to do greenwashing; where a company claims their product to be more sustainable than it actually is. This leads to consumers believing they are making sustainable purchases when in reality they are contributing to damaging the environment as much as any other filament.
Summary
To recap and round up, recycling 3D-printed waste poses multiple challenges. Recognition of waste in a large stream, collecting and offering pre-sorted waste to filament manufacturers, recycling filament itself, and the education, legislation and environment around it. While 3D-printing waste specifically may not be significant enough in comparison to other waste streams, this market will see a significant growth. To minimize the environmental impact now and in the future, research must be done, and improvements must be introduced as soon as possible if we wish to reduce the impact of plastics from a growing market.
If this article has inspired you to read more about this problem specifically, or about FIP-AM@UT itself, I’d like to put one of our projects in the spotlight. The FIP-AM@UT has contributed to the project Waste2Print (https://fip.utwente.nl/nl/project/waste2print/). Together with companies Riwald Recycling and 3devo, we focused on turning polymer waste into 3D-printer filament, to make new products that are also recyclable. In addition, we’re always looking for new project partners to work on current (or future!) manufacturing challenges. If you’d like to know more about how we can be of help, please visit our website or reach out on social media, and we’ll get in touch with you.
Thank you for reading this blog.