
Mobile Robotics: Applications, and Capacities
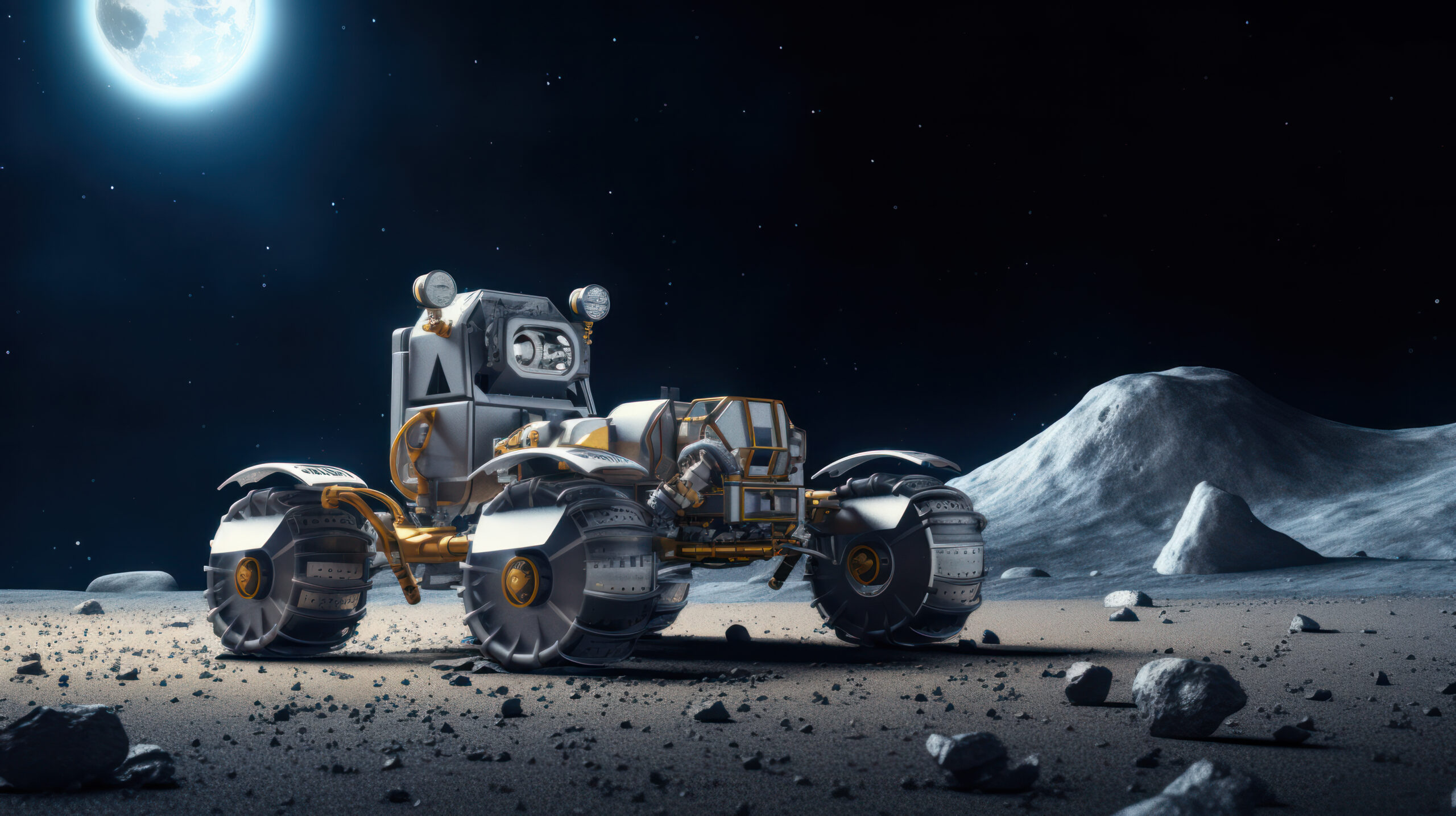
The common industrial robots are typically stationary, featuring a jointed arm (articulated manipulator) and gripper attached to a fixed surface. Mobile robots possess the ability to navigate freely in their surroundings and aren’t confined to a single location (1). The advent of Mobile Robotics introduced a new chapter in the world of intelligent systems by providing more flexibility and autonomy. The Applications of Mobile Robotics cover a wide range from smart inventory systems to space explorations (Rovers) and rescue operations. Mobile Robots are mainly categorized based on their mode of motion (locomotion), namely, Wheeled Mobile Robots (WMR), Legged (walking) Mobile Robots (LMR), Tracked Locomotion Mobile Robots, Air-based and Water-based (2).
WMRs are the most mature type of mobile robot since transportation with wheels has been the main locomotion method for other types of mobile systems (e.g. trains and cars). Accordingly, the Automated Guided Vehicle (AGV) has gained a reputation for being used as an automatic material-handling system. The Autonomous Mobile Robot (AMR), which is the more advanced version of AGV, is designed to perform defined tasks independently. The AMRs are programmed to reach particular locations and can find new paths towards the final destination. The applications of such smart systems cover different sectors such as material handling, maintenance, and agriculture. The factor separating the AMR from other mobile systems is its robustness in unpredictable circumstances. For example, when an obstacle blocks the robot’s path, it can calculate a new path that is still accessible.
Figure 1 Avidbots Neo autonomous floor cleaning robot. | Credit: Avidbots
Another domain within mobile robotics is the Legged Robots. Being inspired by animals and humans, they are developed to deliver a similar locomotion principle. While the capabilities of WMRs heavily depend on the surface on which the wheels are rolling, the Legged Robots are capable of overcoming uneven surfaces, climbing, and functioning on non-rigid terrains (e.g. mud, sand, and snow). One of the pioneering companies in this field is BostonDynamics (3).
Figure 2. Spot Robot, Credit: BostonDynamics
It is beneficial to mention that the combination of WMRs and Legged Robots is known as Wheel-Legged Mobile Robots (WLMR). This type of robot uses the hybrid characteristics of wheels to travel swiftly and uses the leg joints to increase the flexibility of motion. In space exploration missions, the energy consumption rate is critical and besides, the probe robot needs to perform versatile tasks, therefore, integrating the benefits of rolling and walking makes a difference (Fig. 3). WLMRs can be assigned to a more generic category of mobile robots called Reconfigurable Mobile Robots (4). The Reconfigurable Robots are mainly used when the uncertainty of the working environment requires mechanical adjustments such as dimension adjustment and locomotion switch. The mechanical reconfiguration helps the system to climb steps, skip the gaps, and overcome deformable paths (e.g. sand or snow).
Figure 3. Mars 2020, Credits: Image: NASA/JPL-Caltech
Gathering information from the environment and act accordingly are the factors that separate robots from other ordinary machines. The mechanical structure of mobile robots, particularly WMRs, has advanced considerably. However, the sensory and decision-making units are being improved constantly to meet the expectations of mobile robots. The most crucial sensors for mobile robots are the State Estimation, Motion Control, Object Recognition, and Ranging sensors which are used for different types of mobile robots (5). The received data from the sensors are employed to generate different motion actions such as navigation, path planning, and obstacle avoidance. The recent maturity in Artificial Intelligence and image processing can provide mobile robots with an extensive range of information about their environment. Conclusively, mobile robots can be operated in environments where the situation changes dynamically.
Sources: