What post-crisis manufacturing will look like
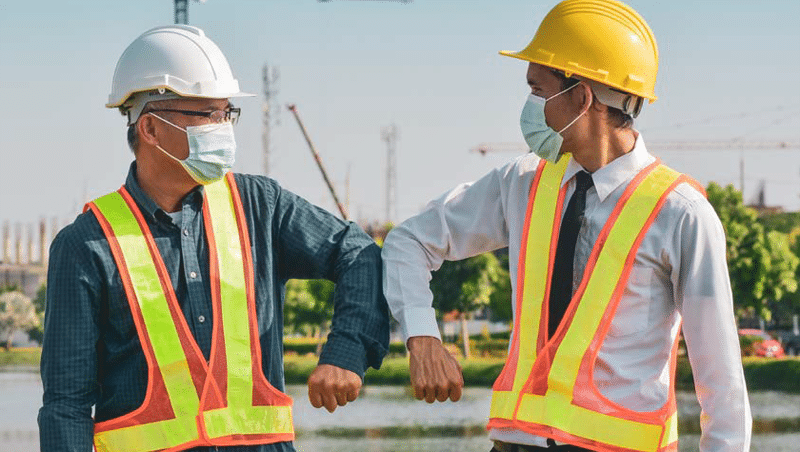
How short-term measures taken in response to the global pandemic will lead to the long-term transformation of the manufacturing sector.
If history has taught us anything, it’s that solutions adopted in response to global crises tend to result in long-term change. The transformation of the manufacturing sector was already well under way before the pandemic. Now the adoption of new technologies is diverging between those which will thrive after the pandemic, and those which won’t.
The pandemic hit manufacturers in an unprecedented way. Stay-at-home mandates suddenly forced factories to send everyone home who could do their jobs from home, and global supply chains continue to see enormous disruption due to travel bans and other restrictions. While we’re all hoping things will go back to normal sooner rather than later, there are some things that will never be the same. And that’s not necessarily a bad thing.
It’s time for manufacturers to embrace the fourth industrial revolution. The pandemic has made that need clearer than ever. Manufacturers need to look beyond today’s uncertain climate and prepare for long-term changes across the industry. The trends we explore below were well-established some time ago, but now it’s time to accelerate their adoption.
Normalisation of remote work and collaboration
With the exception of lights-out manufacturing facilities, shop floors still require employees to be physically on-site. However, social distancing measures have forced many plants to reduce the size of their on-site teams, retaining only a skeleton crew to operate, maintain, and repair machines.
Of course, many manufacturers are still a long way from adopting a lights-out methodology, but that doesn’t mean they can’t benefit from adopting a long-term remote work environment. For example, manufacturers with large customer service departments might consider shifting to permanent remote work empowered by digital communication and collaboration platforms. The same applies to
a myriad of other office roles, such as those in finance, administration, marketing, or supply chain management.
The reduction in workers on the shop floor has also highlighted the value of remote diagnostic and management tools. Thanks to internet-connected industrial control systems, it’s possible to integrate real-time data collection and AI-driven insights into cloud collaboration platforms. Specialists can even control certain operations on the shop floor remotely. Remote work isn’t just for back-office roles anymore. It’s also a new reality that will fundamentally transform manufacturing.
Rethinking manufacturing supply chains
Supply chains continue to face enormous stress, not just because of COVID-19, but also due to the looming possibility of a global trade war. Furthermore, pandemic-induced recession has forced many suppliers out of business and will continue to do so. Manufacturers, particularly those with complex global supply chains, are now focusing on ensuring continuity throughout the crisis. However, it’s also important to think beyond.
For too long has manufacturing been focussed on obtaining supplies at the lowest possible price. The pandemic, compounded by political tensions and rising environmental concerns, has revealed the fundamental flaws in that model. Today, consumers are increasingly wary of what they buy, including how and where it was made. Price is no longer the main purchase driver for many people. These factors continue to drive a steady shift from globalisation to regionalisation.
As part of a long-term response to the aftereffects of the pandemic, governments are likely to promote domestic manufacturing as part of their plans to increase resilience of manufacturing sectors considered critical for national sustainability. Some governments are already offering incentives to firms to bring their manufacturing back home. Even those which don’t operate in sectors deemed essential, pressure to turn towards domestic suppliers will likely continue to grow.
Development of automation technologies
The consumer market has been taking advantage of cheap everyday goods for years thanks to these global supply chains, but the revival of domestic manufacturing doesn’t have to mean dramatic price increases. Thankfully, advances in technology mean it’s possible to replace the race-to-the-bottom low-skilled labour costs with automation and machine learning. In fact, this should create many new job opportunities for skilled workers.
The human factor will always remain a core element of manufacturing operations. Automation replaces many low-skilled job roles, and it will continue to do so. At the same time, it leads to an increased need for digitally savvy workers. Manufacturers should focus on reskilling their workforces to prepare for these changes. Following Toyota’s principle of ‘autonomation’, 10 to 20% of the manufacturing process should be addressed by human expertise, while the rest is automated.
COVID-19 is already sparking a new wave of automation and robotics on the shop floor. These systems augment the capabilities of human teams, and many can be managed remotely. Once the crisis is over, manufacturers may experience dramatic and often unpredictable fluctuations in demand, with packaging and logistics requirements liable to change at a moment’s notice. Automation can help respond to these needs quickly, efficiently, and with little or no additional cost. Not only does this keep disruption to a minimum – it also gives manufacturers the chance to capitalise on opportunities which they might otherwise have missed.
Final words
Flexible manufacturing won’t just support the industry’s recovery from COVID-19 – it will help firms prepare themselves for an uncertain future ahead. The rapid deployment of adaptable manufacturing processes brings many benefits which will be realised for many years to come:
- Improved manufacturing efficiency
- Enhanced workforce productivity and morale
- Decreased operational and business risk
- Reduced waste and environmental impact
- Better worker health and safety
Crises have always driven innovation across the manufacturing sector, and today’s pandemic is no exception. While the hardships wreaked by COVID-19 are undeniable, it’s also a tragedy that highlights the opportunity for people and machines to work better and innovate together.