
Additive Manufacturing: an emerging hero in crisis situations
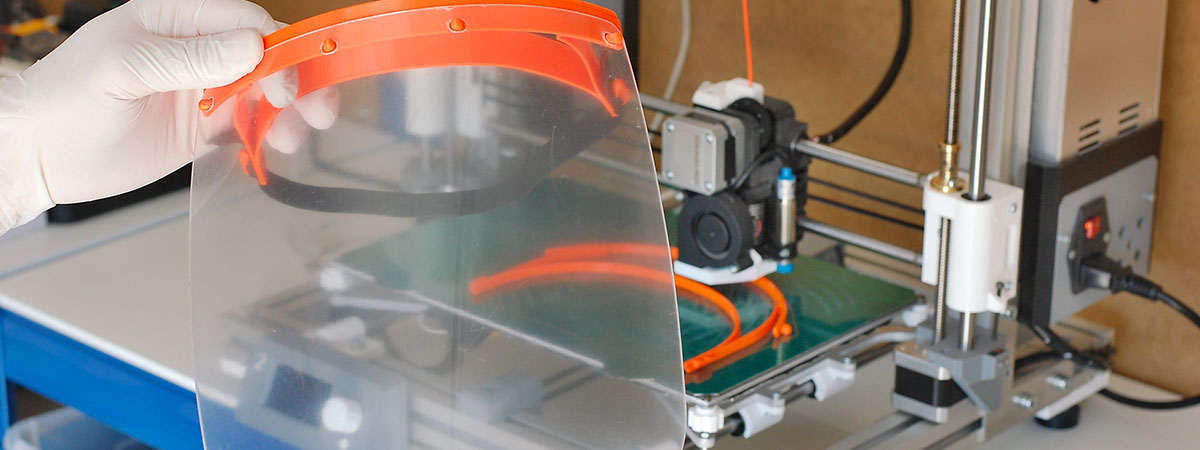
Additive manufacturing technologies have rapidly become a vital tool in assisting in response to the current COVID19 virus crisis. Many countries around the world are seeing their healthcare systems completely overwhelmed, with nurses and doctors being called out of retirement to care for patients and test huge populations for the novel virus. Due to the overwhelming medical response required, many areas are beginning to see serious shortages of vital medical equipment for patients and personal protective equipment (PPE) for healthcare staff. It is becoming evident that relying on international supply in a time of global crisis presents serious issues.Mainly due to the reason that manufacturers of equipment and protective gear, who are already struggling to meet demand are being ordered to keep stock for domestic internal use,
Additive Manufacturing – A new vital tool in the fight to save lives
However, in many regions additive manufacturing at the smallest of scales has become an unexpected solution to mass supply shortages, in what is increasingly becoming a wartime-like effort.
Online 3D printing communities, such as social media groups on Facebook have rallied together to help with the supply of medical equipment. Through 3D file-sharing databases such as Thingiverse and GrabCAD, designers and owners of 3D printers are collaborating to rapidly design and manufacture equipment, to be donated to hospitals and healthcare workers.
Some of the most basic designs are proven to be the most useful. PPE such as faceguards or shields are vital in stopping airborne droplets contacting medical staff during treatment and testing of patients. FDM printers are being used to create simple headbands, that coupled with a thin sheet of cut plastic such of polycarbonate or acrylic becomes a perfectly functional PPE item at extremely low cost. Individuals are even printing these parts in their homes and garages and delivering or posting boxes to central collection points for packaging and delivery to hospitals.
On the more advanced side, hospitals are using their own equipment or those of partnered research institutes to produce venturi ventilator valves using technologies such as polymer sintering. In the USA, the University of South Florida are 3D printing nasal swabs on FormLabs SLA machines in great numbers to be used in the testing of COVID-19. Another example is in Brescia, Italy where hospitals were facing extreme ventilator shortages with people dying in wait. Cristian Fracassi and his team volunteered their time and expertise to produce unofficial replica valve parts to greatly increase the hospitals intensive care ventilator capacity.
Due to the extreme urgency of the situation, with people’s lives depending on equipment being available many hospitals, and manufacturers alike are skipping the long formalities and bureaucracy required behind producing medical related equipment. Intellectual property of part designs and the testing and medical certification of parts are largely being ignored in the short term due to the simple fact that without this equipment, many people are dying or being put at risk daily. Without this vital equipment, more people will die.
Manufacturers with 3D printing capability from unrelated industries are also being called up by governments to help in the wartime like effort to combat COVID-19. In a similar style, design communities around the world are starting to open funded competitions. Asking for design entries for simple, affordable, and effective equipment such as mechanical medical ventilators. Medical ventilators are a critical piece of equipment in assisting patient breathing in severe cases of virus induced pneumonia.
On the other side of this terrible virus that has changed the world, we expect to see additive manufacturing technologies become more common place and have a greater role in our hospitals and medical supply chains.
Think you can help?
If you are reading this, have additive manufacturing capabilities and are wondering what you can do to help, please consider the following. Reach out to your local University, industry group, industry professional body or government manufacturing body. Many governments around the world are now calling on businesses with manufacturing capability to help alleviate unprecedented demand of various types of basic PPE and medical equipment supply. Some of the most basic supplies such as mask clips and face shields are what is most in need and can be manufactured using common 3D printers.The Fraunhofer Project Center at The University of Twente has recently become involved with the Give-a-breath challenge to create a low-cost, easily constructed and freely available ventilator design using Additive Manufacturing.